After more than 20 years working in technology, Jared Haworth saw the light — neon, that is.
Growing up just outside NYC, along U.S. Route 1, meant that some of Haworth’s “earliest memories are of the neon signs along that road down into New York.”
And this interest never dimmed, as in the intervening years Haworth sought out neon signs to photograph before being turned on to a sign-making class at Nate Sheaffer’s Glas, a fixture in the Raleigh neon scene. After Haworth’s first foray into glass bending, he was spending enough time in the Glas studio to switch to working there as a full-time glass bender and sign maker.
Prior to Sheaffer’s retirement, he offered Haworth the opportunity to learn the business side of operating a neon shop as studio manager. “Despite Glas’s impending closure,” Haworth said, “our crew felt that there was still a strong market for all things neon here in central North Carolina.”
Now several months into his post as skipper of Lightship Neon, (leaning into the nautical puns) Haworth and his team of skilled craftspeople bring customers’ neon ideas to life — and light — by creating custom neon signs for businesses and individuals, performing repairs and restorations for existing signs, and teaching workshops to spread awareness and appreciation for neon.
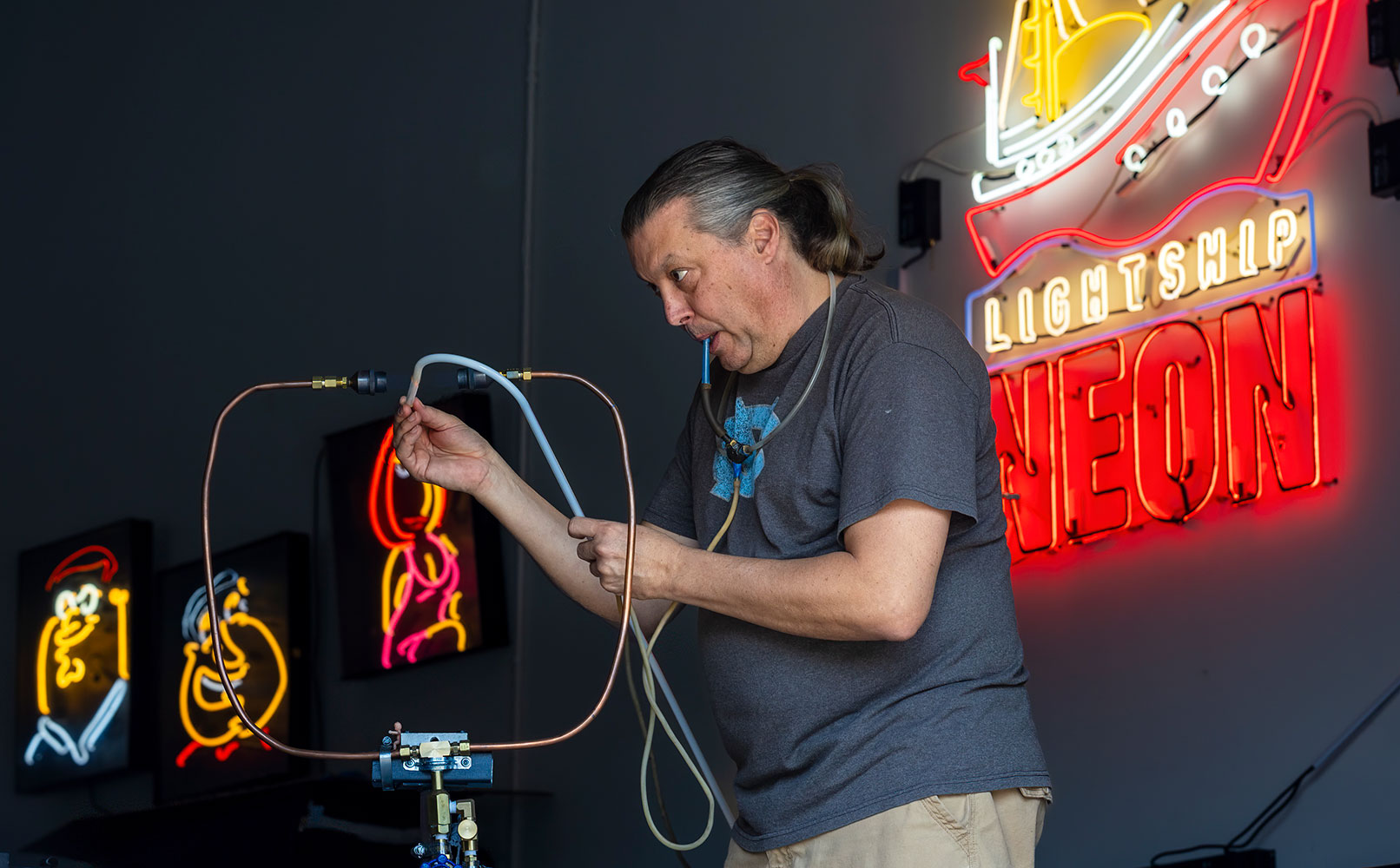
Marvill’s bending of glass has taken thousands of hours to master.
The unique and eye-catching functional art form has followed a pattern of rises and drops in popularity from LA’s first commercial signs in 1923 until the LED technology of the 2000s eclipsed neon lighting as the dominant form of illumination in advertising. In recent years, neon has seen another resurgence — though for artistic and custom, one-off purposes rather than large-scale commercial projects.
We recently met with Haworth, who enlightened us about neon and the Lightship shop.
Can neon be used for more than signs?
Absolutely! Luminous tubes, filled with neon or argon gas, are a diffuse lighting source that fills a space with inviting light in a way that can’t be matched by LEDs. Neon tubes can also be used artistically to create recognizable or abstract shapes, be wrapped around three-dimensional objects as accents, or even made into long, straight tubes to border and light up a space.
Why the name Lightship Neon?
My childhood included trips to Nantucket Island, where I had the opportunity to tour a former operational light vessel, United States lightship Nantucket (LV-112). Even North Carolina had its own lightship, at Frying Pan Shoals (LV-115), prior to the construction of the uncrewed platform there today. I loved the concept of a floating lighthouse, guarding dangerous approaches to land, staffed by a dedicated crew operating their light beacon for all to see.
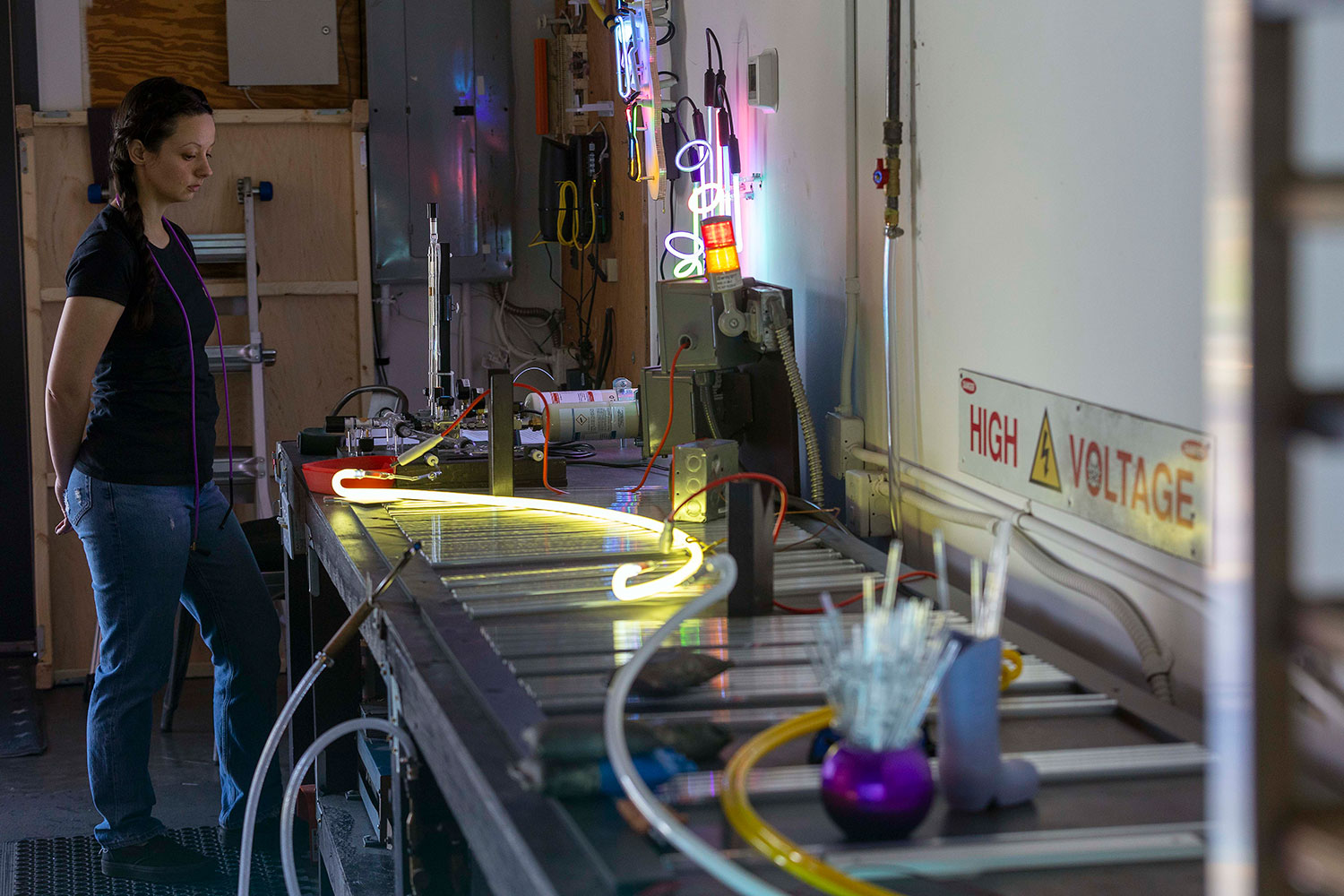
Hypes powers up the transformer’s 24,000 volts of electricity.
Tell us about the team.
We’re currently a crew of three: myself, Richard “Rich” Marvill, and Kendra Hypes. Rich is our main glass bender — almost every sign created in our workshop features his work exclusively. Rich, who has been my mentor throughout my glass-bending journey, also teaches aspiring sign makers, performing the glass-bending demonstration and narrating the tube bombarding and gas-filling process. Kendra was the primary tube processor at Glas, where she operated the vacuum manifold and bombarding transformer to bring each neon tube to life. She continues that role at Lightship, where she helped to define the 43-step instruction guide that ensures each tube enters the world with the best chance of a long service life. Kendra, herself an emerging neon artist, also assists in hands-on classes by supervising students in the fires and guiding them to create the glass needed to bring their designs to life.
Describe the Lightship Neon space.
While every neon shop has similar equipment (almost all of ours being secondhand, some of it decades old, as the craft of neon sign making hasn’t changed much since its inception), each shop adopts their own practices and processes. One of the great things about our space was that we were handed a blank canvas and were able to lay everything out so that tubes move from bending to processing to painting to assembly, with all tools and materials close at hand. We also have a dedicated showroom/lobby, where we introduce neon and showcase recently completed custom work before throwing open the workshop’s double doors and revealing the magic behind the signs.
Lightship Neon classes are a great way to participate in creating a custom, one-of-a-kind sign!
Workshops currently offered:
- Half-day on Monday afternoons and evenings (or as private classes by special arrangement)
- Multi-week intensives across four Wednesday evenings
Lightship Neon also offers corporate and team-building opportunities, and all workshop participants can rent time in the shop to work on personal projects.
Tell us about a cool project you’ve worked on!
The neat thing about working in a neon sign shop is that no two projects are alike. While I’m immensely proud of our larger-scale work, one of the coolest projects was for a freelance creative director working for CBS Sports who commissioned us to make a neon accent for The NFL Today Super Bowl Pregame Show logo. It was incredible, tuning in to CBS and seeing our work right there on TV!
What’s your hope for Lightship Neon?
It’s twofold: I’d love for us to make our mark on the Raleigh area, as we’re already able to drive through the city and see our work on display in and on various buildings; continuing that is a priority. The second, and possibly more important, goal is to continue to spread the excitement and enthusiasm for neon through our workshops and events, as we do our part to keep this art form alive.
- Garden Adventurer: Landscaping with Spiders
- Out & About in Wake County: May/June 2024
- Pursuing Greatness
- Splash Into Summer
- Go Big
- Lightship Neon
- Pay it Forward: Artspace
- Erica Chats: Spring into Summer Fashion
- Celebrated Spirits: SHIfT NEIPA
- Celebrated Spirits: Hummingbird
- Your Perfect Wake Picnic
- The Making of a Fashion Designer